
CNC Machining: A Key Driver of Precision Manufacturing
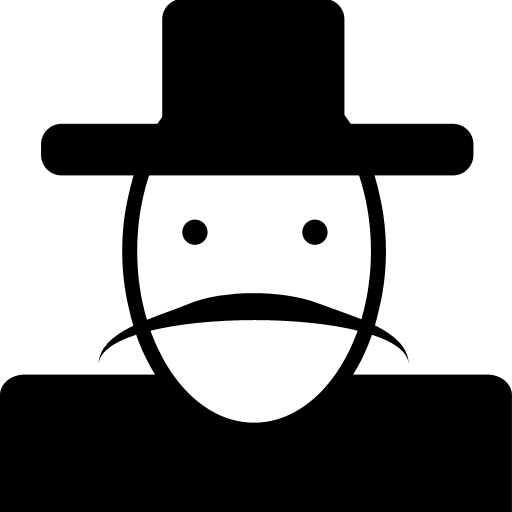
Computer Numerical Control (CNC) machining has become a cornerstone of modern manufacturing, revolutionizing industries by providing high precision, efficiency, and flexibility. With CNC technology, businesses can produce complex parts with a level of detail and consistency that was once impossible to achieve using traditional manual methods. This article explores the significance of CNC machining, its advantages, and how it has transformed the manufacturing landscape.
What is CNC Machining?
CNC machining is an advanced manufacturing process where computer software dictates the movement of factory tools and machinery. The process can control a wide range of machines, such as grinders, lathes, mills, and CNC routers, enabling them to carry out various dimensional tasks with exceptional accuracy. Unlike traditional methods, where operators manually adjust machinery using levers and buttons, CNC machining automates the entire process, eliminating the potential for human error and improving overall efficiency.
At the heart of CNC machining lies the programming of the system. The operator inputs a detailed set of instructions into the computer software, which then directs the machines to make precise cuts or shapes as needed. This ability to perform multi-dimensional cutting tasks in one continuous process is one of the key factors that sets CNC machining apart from manual machining.
The Process of CNC Machining
The CNC machining process begins when the desired design is translated into a program that tells the machine what to do. The design is typically created using Computer-Aided Design (CAD) software, which provides a digital representation of the part to be manufactured. This design is then converted into a set of instructions known as G-code, which the CNC machine follows to achieve the required dimensions.
One of the primary benefits of CNC machining is its precision. Once the program is in place, the machine can operate continuously without the need for human intervention, producing parts that are identical in quality every time. This is especially important in industries where tight tolerances and high-quality standards are critical, such as aerospace, automotive, and medical device manufacturing.
Advantages of CNC Machining
The rise of CNC machining has provided several significant advantages to manufacturers. First and foremost, it improves the accuracy and consistency of parts. CNC systems can execute detailed tasks with minimal error, ensuring each part meets exact specifications. Additionally, the process is much faster than manual machining, as CNC machines can run for extended periods without interruptions, increasing production speed and output.
Another major advantage is the flexibility that CNC machines offer. As manufacturing needs change, the software can be updated with new instructions, allowing the machines to adapt to different designs or production requirements quickly. This flexibility reduces downtime and helps manufacturers stay competitive in a rapidly changing market.
CNC machining also enhances worker safety by reducing the need for manual intervention. With machines performing tasks autonomously, operators are less exposed to potential hazards, such as sharp tools or high-speed machinery. Furthermore, the automation provided by CNC systems allows for more streamlined operations, freeing up employees to focus on other critical tasks within the manufacturing process.
The Role of CNC Programming
CNC programming is a crucial aspect of CNC machining. The code used to direct the machine is written and edited by CNC programmers, who create detailed instructions that dictate the machine’s movements. These instructions are then input into the machine’s computer system, where they are stored and executed when needed.
Programming CNC machines requires a high level of expertise, as the code must be precise and free from errors. Modern CNC programming systems have become more intuitive, making it easier for operators to modify and update programs as needed. This ability to adjust the programs ensures that the machines can handle various tasks without requiring significant downtime.
The Future of CNC Machining
CNC machining has already had a profound impact on the manufacturing industry, but its potential is far from fully realized. As technology continues to advance, CNC systems are becoming more sophisticated, offering even greater control and flexibility. Future developments may include machines that can work with more advanced materials or perform tasks that were previously outside the scope of traditional CNC machining.
The integration of artificial intelligence and machine learning into CNC systems could further enhance the precision and adaptability of CNC machines, allowing them to optimize their performance based on real-time data and feedback. This could lead to even faster production times, reduced waste, and more efficient manufacturing processes.
In conclusion, CNC machining has transformed modern manufacturing, providing unmatched precision, efficiency, and flexibility. As technology evolves, the role of CNC machines will continue to grow, helping industries meet the demands of an increasingly complex and fast-paced world.
Key Advantages of CNC Machining
Advantage | Description |
---|---|
Precision | CNC machines provide consistent, high-quality results, minimizing human error in manufacturing. |
Efficiency | Machines can operate continuously, increasing production rates and reducing labor costs. |
Flexibility | CNC programs can be easily modified to accommodate different designs, enhancing adaptability. |
Safety | Reduces the need for human intervention, improving workplace safety by automating hazardous tasks. |
Speed | CNC machines can produce parts much faster than manual methods, improving lead times and throughput. |
CNC machining continues to be a driving force behind the evolution of manufacturing, offering significant improvements in the precision, efficiency, and safety of production processes.
Comments are closed.