
CAM Software Evolution: From Manual Programming to AI-Powered
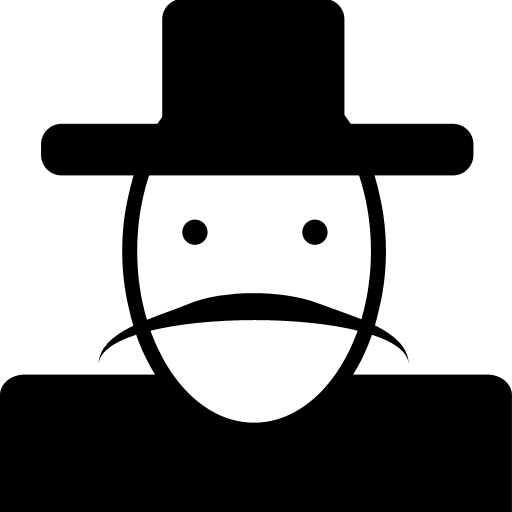
The Shift from Hands-On to Hands-Free
Computer-aided manufacturing (CAM) software has evolved dramatically over the past few decades. From manually inputting G-code to AI-driven toolpath generation, the evolution of CAM reflects the broader digital transformation of manufacturing. Today’s CAM systems not only automate machining instructions, but also become intelligent partners in the design-to-manufacturing workflow, able to adjust toolpaths based on geometry, material, and real-time feedback.
A Brief History of CAM
In the early days of CNC machining, programming was entirely manual. Operators had to write G-code line by line, defining every tool movement with painstaking precision. This process was time-consuming and prone to error.
The introduction of 2D and 3D CAM software in the 1980s and 1990s allowed users to generate code based on digital part models, significantly accelerating the process. However, these systems were rule-based and lacked the ability to make context-aware decisions.
How Traditional CAM Systems Work
Traditional CAM software converts CAD models into toolpaths using a set of defined machining strategies. The process typically involves:
- Importing the CAD geometry
- Selecting machining operations
- Defining tools and speeds/feeds
- Generating toolpaths based on user input and geometry
- Post-processing into machine-readable G-code
While this approach works well for predictable parts, it depends heavily on user expertise and trial-and-error.
The Rise of AI-Powered CAM
Recent advancements in machine learning, cloud computing, and big data have opened the door to AI-powered CAM systems. These platforms don’t just follow instructions—they learn from past jobs, understand context, and adapt strategies to improve performance.
Key Features of AI-Enhanced CAM:
- Automatic recognition of part features (holes, bosses, pockets)
- Adaptive toolpath generation based on material, machine, and cutting dynamics
- Real-time simulation and error detection
- Process optimization recommendations (e.g., reduce tool changes, improve surface finish)
- Learning from historical data to reduce redundant setups
AI Toolpath Planning: What’s Changing?
Aspect | Traditional CAM | AI-Powered CAM |
---|---|---|
Toolpath Strategy | Rule-based | Data-driven, adaptive |
Geometry Recognition | Manual selection | Automatic feature recognition |
Speed & Feed Optimization | User-defined | Auto-adjusted based on simulation/feedback |
Simulation | Static and pre-process | Real-time, dynamic |
Learning Capabilities | None | Learns from past projects and outcomes |
AI-enhanced CAM tools reduce programming time and increase machining efficiency, especially for complex geometries or small-batch runs.
Benefits in Real-World Applications
Industries are already seeing significant benefits from AI-driven CAM technologies:
- Aerospace: Shorter lead times for complex 5-axis parts
- Automotive: Reduced waste in prototyping and mold making
- Medical: Higher repeatability for implant production
- Job Shops: Quicker turnaround for custom one-off parts
Companies using AI-CAM report up to 40% faster programming, 20–30% shorter cycle times, and fewer errors during the cutting process.
Challenges and Integration
Despite the advantages, transitioning to AI-driven CAM comes with challenges:
- Software Cost: AI systems often require higher upfront investment
- Learning Curve: Operators must adapt to new tools and workflows
- Data Requirements: AI depends on high-quality part data and feedback
- Interoperability: Compatibility with legacy machines and CAD files is essential
Manufacturers must consider training, IT infrastructure, and ROI when adopting next-gen CAM platforms.
Looking Ahead: Autonomous CAM
Future CAM platforms will likely incorporate full autonomy. Imagine software that:
- Imports a CAD model
- Identifies machining features
- Selects tools
- Calculates optimal toolpaths
- Simulates and validates the process
- Sends G-code directly to the CNC machine
All with minimal human input.
These systems will rely on cloud-based computing, IoT sensor data, and AI models trained on thousands of machining scenarios. Autonomous CAM could be the foundation of lights-out manufacturing, where entire production cycles run unattended overnight.
The evolution of CAM software from manual programming to AI-powered intelligence represents a critical shift in modern manufacturing. By offloading repetitive and complex tasks to smart systems, engineers and machinists can focus more on innovation and quality.
As CAM technology continues to advance, manufacturers who embrace these changes early will gain a competitive edge in efficiency, flexibility, and scalability.
Comments are closed.