
How Does AI Help Choose the Right Tools in CNC Machining?
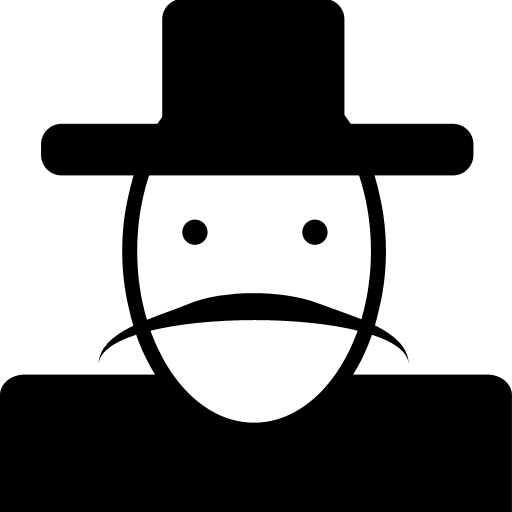
Tool selection is one of the most critical decisions in Computer Numerical Control machining. Selecting the wrong tool can result in poor surface finish, reduced tool life, tool wear, or even complete tool failure. Traditionally, this process has relied on the expertise of skilled operators and engineers. However, with the increasing complexity of production, Artificial Intelligence is stepping in to speed up and optimize tool selection.
Why Tool Selection Matters More Than Ever
Modern CNC operations often deal with:
Diverse materials (from soft aluminum to hardened steel and composites)
Complex geometries (multi-axis contours, undercuts)
Tight tolerances and high throughput demands
In this environment, choosing the most suitable cutting tool—based on material type, toolpath, surface finish requirements, and machine capability—is no longer a simple lookup task. AI offers a solution that scales with complexity.
How AI Approaches Tool Selection
AI-driven tool selection systems leverage machine learning algorithms trained on vast datasets of historical machining jobs, tool performance data, and material behaviors. They integrate multiple sources of information to recommend the best tool for a specific operation.
Key Data Inputs:
Material properties (hardness, machinability)
Tool database (coating, flute geometry, tool length, brand history)
Machine specs (spindle speed, torque limits)
Past job performance (tool wear rates, surface finish outcomes)
How the AI Works:
Analyze CAD/CAM model: Understand geometry, features, tolerances
Match with historical data: Search for similar tool-material-job combinations
Predict outcomes: Simulate cutting forces, tool life, and chip load
Rank and recommend: Offer top choices based on performance, cost, and efficiency
Traditional vs. AI-Driven Tool Selection
Feature | Traditional Method | AI-Driven Selection |
---|---|---|
Based on | Human expertise and handbooks | Historical data + predictive models |
Speed | Slower (manual lookup and judgment) | Fast (automated analysis in seconds) |
Accuracy | Highly variable (experience-dependent) | Consistent and data-backed |
Adaptability | Limited | Learns from new jobs and outcomes |
Material-specific tuning | Often generic | Highly customized recommendations |
Case Study Example: Titanium Machining
Problem: A manufacturer faced high tool breakage rates when milling aerospace-grade titanium.
Traditional Approach: Used conservative speeds/feeds from manufacturer catalogs.
With AI Tool Selection:
System analyzed over 200 past titanium jobs
Identified a coated carbide end mill with specific helix angle
Recommended reduced radial depth with increased speed
Result: 37% longer tool life, 12% cycle time reduction
Visualization: What AI Considers
AI-Based Tool Decision Matrix
Factor | Weight (%) | Example Consideration |
Material Type | 30% | Titanium vs. Aluminum |
Tool Geometry | 25% | Number of flutes, helix angle |
Machine Capability | 20% | Max RPM, feed rate control |
Tolerance Demands | 15% | ±0.01 mm requires fine finishing tools |
Surface Finish Goal | 10% | Mirror vs. matte finish |
Benefits of AI-Based Tool Selection
Reduced Setup Time: Engineers no longer need to spend hours matching tools manually
Improved Tool Life: Optimized parameters minimize wear and breakage
Enhanced Surface Quality: AI fine-tunes tool type for desired finish
Fewer Human Errors: Decisions are based on validated outcomes
Scalability: Ideal for high-mix, low-volume production environments
Implementation Considerations
Software Integration: AI modules must connect with existing CAM software and machine controllers
Data Quality: The AI is only as good as the machining and tooling data fed into it
Operator Trust: Shop-floor teams must trust and validate AI recommendations
Cost vs. ROI: Advanced systems require investment, but pay off in efficiency and quality
Is This the Future of Machining?
As digital manufacturing evolves, AI tool selection is moving from an experimental concept to a competitive advantage. In the near future, we can expect:
Real-time AI adjustments during machining
Autonomous tool changing based on sensor feedback
Integration with digital twins for full job simulation and optimization
AI won’t replace human machinists—it will empower them. By automating the complexity of tool choice, manufacturers can focus on innovation, product quality, and faster delivery.
Stay tuned to MachinemanFuacturer for more insights into how smart technologies are transforming machining workflows—from the spindle to the shop floor.
Comments are closed.