
AI-Driven CNC Machine Tools: Shaping the Future of Smart Manufacturing
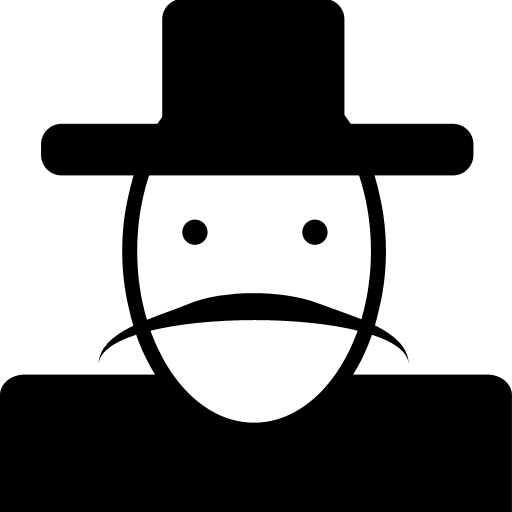
Introduction: A New Era in CNC Machining
The global manufacturing industry is undergoing a transformation with the advent of AI-driven CNC machines. These smart machines not only improve production efficiency, but also provide adaptive learning, predictive maintenance, and real-time decision-making capabilities on the shop floor. As industries pursue precision, speed, and reduced downtime, AI-driven CNC machines are becoming a key enabler of Industry 4.0.
Why AI in CNC Matters
Traditional CNC machines, while precise and reliable, operate on pre-programmed paths. In contrast, AI-enhanced systems adapt to sensor feedback, tool wear, and environmental variations in real time. The result is a leap in autonomy, efficiency, and error reduction.
Key Comparison | Traditional CNC | AI-Powered CNC |
---|---|---|
Programming | Manual G-code | Self-optimizing algorithms |
Maintenance | Scheduled | Predictive & condition-based |
Error Handling | Reactive | Proactive error prevention |
Flexibility | Low | High (adaptive to part variations) |
These capabilities make AI-enhanced CNC tools particularly valuable in aerospace, automotive, and medical device manufacturing, where tolerances are extremely tight and material costs are high.
Core Technologies Behind AI-Powered CNC Machines
- Machine Learning Algorithms:
These allow machines to analyze production data, optimize cutting paths, and reduce unnecessary movements. Commonly used algorithms include supervised learning for toolpath optimization and unsupervised learning for anomaly detection. - Computer Vision:
Integrated cameras and image processing help machines detect defects, misalignments, and deviations in real-time. AI systems can then adjust machining parameters accordingly. - Digital Twins & Simulation:
AI can simulate machining processes before production begins, using digital twins to anticipate tool failures and reduce trial-and-error setups. - Edge AI Chips:
These embedded processors enable real-time computation at the machine level, cutting down latency and reducing dependence on cloud-based systems.
Real-World Applications and Case Studies
Automotive Sector
A major German automaker recently deployed AI-driven CNC milling machines in their EV motor housing production line. The AI system automatically adjusts for aluminum casting variations, reducing scrap rates by 22% and improving tool life by 30%.
Aerospace Precision
In the aerospace sector, a U.S.-based manufacturer integrated AI-enabled CNC grinders for turbine blade production. Using real-time feedback, the system ensures sub-micron accuracy, compensating for tool deflection during the grinding process.
Medical Devices
AI-powered turning centers in orthopedic implant factories are transforming production. These machines dynamically adjust for micro-variations in titanium bar stock, reducing the rejection rate of high-cost medical implants.
Challenges and Limitations
While promising, AI in CNC machining isn’t without challenges:
- Data Dependency: Large volumes of high-quality data are required for effective model training.
- Integration Cost: Upgrading legacy systems with AI capabilities can be costly.
- Skill Gap: Operators and technicians must understand AI basics to fully leverage these systems.
Challenge | Description | Possible Solution |
---|---|---|
Data Quality | Noisy or inconsistent sensor data can mislead AI models | Implement standardized data acquisition protocols |
Legacy Systems | Old machines lack sensors and computing capabilities | Retrofit kits or hybrid integration strategies |
Skills | Operators may lack training | Upskill programs, workshops, and online certification |
The Market Landscape and Future Outlook
According to MarketsandMarkets, the global AI in manufacturing market is expected to grow from USD 2.3 billion in 2023 to over USD 16.7 billion by 2030, with AI-powered CNC machines being a significant contributor.
Key industry players like Siemens, Fanuc, and Okuma are investing heavily in R&D, focusing on cloud integration, autonomous quality inspection, and collaborative robotics (cobots) that complement CNC operations.
Future Trends to Watch:
- AI + IoT (IIoT): Full integration with factory IoT platforms for data-rich, autonomous machining.
- Voice & Gesture Interfaces: Operator-friendly human-machine interaction.
- Self-Healing CNC Systems: Machines that detect, diagnose, and correct internal faults without human intervention.
Smart Manufacturing is Here to Stay
AI-powered CNC machines are not just a trend—they’re a necessity for manufacturers aiming to stay competitive. As these technologies evolve, even small-to-medium enterprises will find scalable solutions that bring intelligence, efficiency, and flexibility to their production lines. For now, the race is on for manufacturers to upgrade their operations and embrace a smarter, data-driven future.
Comments are closed.