
What Is AI-CNC? Beginner’s Rule to Smart CNC Machines
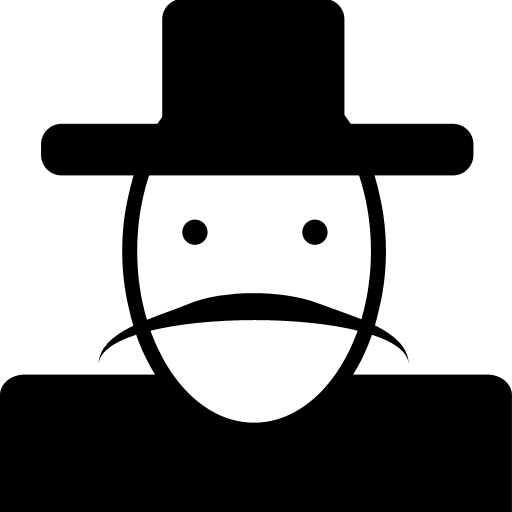
Introduction: A New Chapter for CNC Machines
CNC machines, or Computer Numerical Control machines, have long been the backbone of modern manufacturing. From milling and turning to drilling and cutting, these machines offer speed and precision unmatched by manual tools. But as the demand for more flexible, smarter, and self-optimizing systems rises, a new generation is emerging—AI-CNC.
So what exactly is AI-CNC? How does it work? And why is it important for the future of manufacturing? This guide breaks it down for you.
What Is AI-CNC?
AI-CNC refers to CNC machines that are powered by artificial intelligence technologies such as machine learning, computer vision, and predictive analytics. Unlike traditional CNC machines that rely solely on pre-programmed instructions, AI-CNC systems can learn from data, adapt to changes, and even make real-time decisions during operation. This integrated technology enables automatic programming, optimization, and real-time adjustments during the manufacturing process, thereby increasing efficiency, accuracy, and overall productivity.
In simple terms, AI-CNC is what happens when CNC machines get smart.
Key Technologies Behind AI-CNC
1. Machine Learning
AI-CNC systems use historical data from past machining jobs to optimize future performance. The machine can “learn” from results to fine-tune parameters such as feed rate, spindle speed, or cutting depth.
Example: If a tool wears out faster while machining a specific material, the system can detect this and adjust parameters to extend tool life.
2. Computer Vision
Equipped with cameras and sensors, AI-CNC systems can “see” the part they are machining. This enables real-time error detection, alignment verification, and surface inspection.
Example: Detecting whether a part is properly clamped or identifying surface scratches before continuing the process.
3. Predictive Maintenance
AI can monitor vibration, heat, torque, and other sensor data to predict when a component (like a spindle) might fail—before it actually does.
This minimizes unplanned downtime and reduces costly repairs.
4. Autonomous Decision-Making
AI-CNC machines can adjust toolpaths and speeds in real time based on feedback from the material being processed.
This results in better finish quality and less material waste.
Traditional CNC vs. AI-CNC: What’s the Difference?
Feature | Traditional CNC | AI-Enhanced CNC |
---|---|---|
Programming | Manual G-code input | Self-adjusting parameters |
Feedback Loop | Limited or none | Real-time sensors and decisions |
Maintenance | Periodic and manual | Predictive and automated |
Adaptability | Fixed logic | Learns and evolves |
Operator Input | High | Lower; system handles optimization |
How AI-CNC Works: A Simple Flow
Here’s a simplified process of how an AI-CNC machine operates:
- Receive Design Input (CAD/CAM file)
- Run Initial Simulation using past data to predict optimal settings
- Begin Machining with real-time sensor monitoring
- Adjust Automatically based on surface finish, temperature, or vibration
- Detect Anomalies using computer vision or audio cues
- Finish Job & Analyze Results to improve the next cycle
Real-World Applications of AI-CNC
Automotive
- Manufacturers use AI-CNC to machine complex engine parts with minimal error. AI helps in adjusting for material variations in aluminum castings.
Aerospace
- Aircraft turbine blade machining demands sub-millimeter precision. AI ensures compensation for thermal expansion and tool deflection.
Medical Devices
- AI-driven CNC machines allow for ultra-precise shaping of titanium implants and surgical tools, while also ensuring surface smoothness and compliance.
Benefits of AI-CNC in Everyday Manufacturing
- Higher Accuracy and Consistency:AI algorithms can analyze data and make real-time adjustments to CNC machines, minimizing human error and ensuring consistent precision, even during long production runs.
- Reduced Downtime:AI-powered predictive maintenance identifies potential issues before they cause breakdowns, allowing for timely maintenance and minimizing unplanned downtime.
- Faster Production Cycles:AI optimizes tool paths and feed rates, leading to faster cycle times and increased throughput, ultimately accelerating project completion.
- Improved Quality Control:AI-driven CNC machines continuously monitor and analyze quality metrics, identifying and correcting issues early in the process, minimizing scrap rates and ensuring consistent product quality.
- Data-Driven Insights:AI analyzes vast amounts of production data, providing valuable insights into process inefficiencies, enabling manufacturers to make informed decisions to optimize performance.
- Enhanced Adaptability:AI-powered CNC machines can adapt to design changes and varying conditions in real-time, leading to greater flexibility and customization options.
- Cost Reduction:By optimizing processes, minimizing waste, and reducing downtime, AI-driven CNC machines contribute to significant cost savings for manufacturers.
- Increased Competitiveness:The enhanced efficiency, quality, and flexibility offered by AI-powered CNC machines enable manufacturers to meet growing demands for precision, customization, and faster turnaround times, improving their competitive position.
- Improved Workplace Safety:AI-powered CNC machines can automate tasks that involve hazardous materials or risky operations, reducing the risk of workplace injuries.
- Continuous Production:AI enables CNC machines to operate 24/7, maximizing production output and meeting the demands of mass production.
Challenges in AI-CNC Adoption
Despite its advantages, adopting AI-CNC comes with challenges:
- High Initial Cost: AI sensors, systems, and software add to upfront investment.
- Data Dependency: The machine needs quality historical data to learn effectively.
- Workforce Training: Operators need to understand new workflows and digital tools.
- Integration with Legacy Systems: Many factories use older machines that can’t be upgraded easily.
Is AI-CNC the Future of Smart Manufacturing?
In many ways, yes. As manufacturing evolves into the era of Industry 4.0, the demand for intelligent, self-correcting, low-waste systems will only grow. AI-CNC aligns perfectly with these needs.
Not only large corporations, but also small and medium-sized enterprises (SMEs) can benefit. Many providers now offer modular upgrades or plug-and-play AI add-ons for legacy CNC machines.
AI-CNC is not just a technological upgrade—it’s a transformation in how we think about production. Machines are no longer just following instructions; they are becoming adaptive collaborators in the manufacturing process.
As industries continue to seek greater efficiency, flexibility, and precision, AI-CNC machines will likely become a standard tool on every smart factory floor.
Comments are closed.